 |
MQ SUPERVISOR-2ND SHIFT - Sparks Nevada
Company: NOW Foods Location: Sparks, Nevada
Posted On: 04/30/2024
ESSENTIAL DUTIES AND RESPONSIBILITIES include the following. Other duties may be assigned. Coordinates all inspection activities on the respective shift, including dispositioning of materials. Conducts and documents investigations as necessary. Oversees and monitors the day-to-day operation of assigned area(s) including workflow, management of work in process, job assignments, rotations, etc. to ensure smooth flow and efficient production. Implements quality and process improvement initiatives in conjunction with quality and operations personnel. Develops, recommends, and implements systems, processes, activities to improve inspection and sampling productivity on all shifts. Ensures the availability of adequate materials and supplies necessary to conduct sampling and inspections. Conducts current Good Manufacturing Practices (cGMP) and on-the-job training of MQ personnel and operations personnel where applicable. Assists with customer complaint investigations. Conducts internal audits for cGMP compliance as needed. Performs inspections, as necessary. Performs root cause analysis (RCA) on manufacturing holds/deviations. Provides long term preventative action measures for manufacturing deviations / holds. Assists Packaging and Processing departments with troubleshooting and resolving daily issues. Coordinates the implementation of rework with production personnel and tracks the status of lots that are on HINV status. Tracks deviations and holds and ensures timely completion. Reviews and updates departmental standard operating procedure to assure cGMP compliance. Ensures that polices, safety rules, FSMA standards and GMP's are followed and enforced and that continual improvement is made towards an injury free environment. Actively participates in root cause analysis and other continuous improvement initiatives. Recommends and implements continuous improvement ideas. Ensures key performance indicators in the manufacturing quality area are met or exceeded. Measures productivity on a daily basis, with goal of meeting standards. Supports positive employee relations, fair treatment and respect in all aspects of interaction with employees; address employee concerns/requests in a timely and caring manner; ensures all employees and ideas are respected and valued and their unique and diverse perspectives are leveraged to improve business results. Actively engages in the performance of his/her team through setting objectives and measuring performance. Serves as a coach and mentor to ensure the ongoing development of his/her team. Actively participates in Tier II meetings. Closes Hold and Deviation Investigations in a timely manner. Provides delegation of daily task assignments for the MQ Inspection team. Creates, updates, and reviews Standard Operating Procedures (SOP), Work Instructions (WI), Forms, Master Manufacturing Records (MMR), and other documentation. Informed and held accountable for food safety and regulatory responsibilities. Identifies and immediately notifies management about actual or potential food safety issues. Resolves food safety issues within their scope of work. Complies with safety and GMP requirements. SAFETY RESPONSIBILITY STATEMENT Supports a culture of safe production and exhibits safe work practices. Actively participates in the safety program by engaging in safety activities. Effectively provides and accepts constructive peer-to-peer feedback on safety performance. Adheres to policies, procedures, SOP's, safe work practices, and safety policies and procedures (SPP). Reports ALL workplace incidents to manager immediately. Communicates concerns to manager, reports hazards, and provides input on prevention. Properly uses, wears, and stores Personal Protective Equipment when required. Participates on safety teams and/or completes safety-related activities as part of regular job responsibilities. Responsible for safe work performance in area. Ensures the completion of job safety analyses, safety inspections and employee training. Acts as primary communicator of safe work practices and information to department. Facilitates employees' participation in the safety activity card program and on safety teams. Completes incident investigation reports and submits them to manager by end of shift on which the incident is reported. Conducts safety contacts and documents corrective and preventative actions. Enforces company policies, procedures, SOP's, SPP's and safe work practices. SUPERVISORY RESPONSIBILITIES Directly supervises MQ employees on the shift. Supervises employees in compliance with all production rules, policies, government regulations, company health and safety rules and quality standards. Carries out supervisory responsibilities in accordance with the organization's policies and applicable laws. Responsibilities include interviewing, hiring, and training employees; planning, assigning, and directing work; appraising performance; rewarding and disciplining employees; addressing complaints and resolving problems. QUALIFICATIONS To perform this job successfully, an individual must be able to perform each essential duty satisfactorily. The requirements listed below are representative of the knowledge, skill, and/or ability required. Reasonable accommodations will be made to enable individuals with disabilities to perform the essential functions. EDUCATION and/or EXPERIENCE Bachelor's in a science field and at least 2 years related experience OR minimum five years quality related experience OR an equivalent combination of experience and education. Prior lead experience required. Prior supervisory experience preferred. Experience in quality processes, inspection, and GMP environment preferred. Previous dietary supplement industry experience preferred. Intermediate to advanced computer skills with Word and Excel required. General understanding of quality concepts involved in food and dietary supplement manufacturing and the ability to relate these concepts to any problems that arise. Experience in Lean Manufacturing including 5S and Lean Practices helpful. PERFORMANCE ABILITY Effectively coordinates and leads team in daily activities to meet key performance indicators set by manager, with strong emphasis on employees, safety, food safety and quality. Displays real time critical decision making with available information. Reviews current KPI's to ensure right metrics are being monitored with the right results being delivered. Monitors specific performance and makes proactive decisions on staffing needs to ensure KPI metrics are met. Drives employee based performance through employee involvement and participation, with guidance and coaching from manager. Collaborates with current team and other departments to ensure cross functional concerns and issues from shift to shift are discussed and are addressed in a timely and effective manner. Visible and leads by example on the floor and models NOW's core values, tenets and servant leadership. Consistently follows all company policies and procedures, including all safety policies and procedures. Ability to work at both the 391 AND 395 facilities in Bloomingdale. LANGUAGE SKILLS Ability to read and interpret documents such as product specifications, departmental instructions, and procedure manuals. Ability to write technical reports, business correspondence, personnel reviews and procedures. Ability to effectively present information and respond to questions from groups of managers, employees or visitors. Excellent interpersonal and active listening skills. Verbal and written bi-lingual skills helpful. MATHEMATICAL SKILLS Ability to apply mathematical concepts such as fractions, percentages, averages, ratios, proportions, and the metric system. COMPENTENCIES Safety Awareness - Considers the impact on safety when making decisions and ensures safety is top priority. Acts with Integrity - Demonstrates responsible, ethical and honest behavior and models NOW's core values. Leads Change and Innovation - Challenges the status quo, embraces technology and process improvements, gathers ideas of others, high level of adaptability. Coaches and Develops Others - Builds teams, develops and cares about team members, values and manages diversity, provides candid and constructive feedback. Communicates Proactively and Effectively - Communicates clearly, candidly, directly and concisely. Keeps others informed and listens carefully to input and feedback. Strong verbal and written communication skills. Approachable, relates well to others, engages people and helps them understand change, provides feedback, articulates clearly, and actively listens. Customer-Driven - Servant-minded leader in which excellent service is provided to all customers, sees business through the eyes of the customer, and acts with the customer in mind. Executes with Excellence - Self-driven, action-oriented, drives for results and motivated to accomplish objectives in a fast-paced environment. Displays a strong sense of urgency to meet all business objectives. Sets clear expectations and acts decisively. Flexibility - Prioritizes and shifts direction as business needs require. Maintains a positive attitude and high quality workload. Ability to work a flexible schedule, including off shifts and weekends to support business need. Leads through Positive Influence - Coaches, mentors and trains staff. Leads the work of others. Demonstrates strong character, builds partnerships, takes personal responsibility for developments, acts as role model to others. Problem-Solving - Reacts quickly and appropriately to opportunities and problems and makes sound decisions. Follows up in a timely manner to issues not immediately resolved. Strong analytical skills to troubleshoot and resolve issues while driving towards root cause analysis. Strong decision making, ability to make independent decisions and ability to problem solve complex issues. Identifies multiple solutions and implements the best solution. Quality - Strong attention to detail skills required. Achieves Results through Teamwork - Open to diverse ideas, works collaboratively, holds self and others accountable, and involves others to accomplish individual and team goals. Time Management - Plans and organizes well, multi-task abilities, stays focused on priorities, visualizes and plans for the future, and executes tasks and projects in a fast-paced environment. PHYSICAL DEMANDS The physical demands described here are representative of those that must be met by an employee to successfully perform the essential functions of this job. Reasonable accommodations may be made to enable individuals with disabilities to perform the essential functions. While performing the duties of this job, the employee is regularly required to talk and hear; stand and/or walk throughout the facility; ascend and/or descend stairs; forward bend and squat; use hands to inspect, handle, and feel; and reach with hands and arms. The employee is regularly required to enter information into a computer, handle product in various stages and forms (i.e. raw materials, work in progress, and finished products in liquid, powdered, and tablet forms), in addition to equipment and/or tools. The employee frequently is required to use his/her sense of smell. The employee must regularly lift, move (in some cases drag items), slide, raise and/or place: Lift up to 50 lbs. from 31 inches, carry for 5 feet and return to 31 inches. Lift up to 50 lbs. floor to waist height. Grasp up to 50 lbs. of force. Lift up to 50 lbs. and move box 10 inches to side, then back again at 36 inches. (MQ Sampler role only) WORK ENVIRONMENT The work environment characteristics described here are representative of those an employee encounters while performing the essential functions of this job. Reasonable accommodations may be made to enable individuals with disabilities to perform the essential functions. Works around ingredients such as vitamins, minerals, amino acids, botanicals, etc. and chemicals such as alcohol, that may require respiratory protection. May be exposed to potentially hazardous chemicals and biological materials. Employee works near moving mechanical parts. Frequently exposed to vapors, airborne particles and/or herbal aromas, some classified as allergens or irritants. This position works in all areas of NOW's manufacturing facilities with direct exposure to ingredients (powders and liquids), mixes, (powders and liquids), equipment, and packaging. Frequently exposed to all of the FDA designated major food allergens (Milk, Eggs, Fish, Crustacean shellfish (e.g. crab, lobster, shrimp), Tree nuts (e.g., almonds, walnuts, pecans), Wheat and Soybeans, except for peanuts. As required, works in a loud area that requires hearing protection and other protective equipment to be worn. Ability to travel occasionally, including ability to travel by air. More...
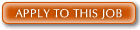
Register an account with us and set up job agents! We'll email you immediately when jobs like this are posted on our site.
|
 |